Crystallinity
In semicrystalline polymers, like in PP, the mechanical properties are mainly determined by the degree of crystallinity. Thus, it is important to understand the variables that define that crystallinity degree of the material.
These variables are basically divided in two big groups. While the first group is composed of the material’s inherent variables such as chains flexibility, regularity and so on, the second group contains those factors related to the material’s transformation, mainly the thermal history and the stress conditions during the processing.
When melted polymer cools, the nucleration and growth of crystals at different points of the sample begin. If the chain is long enough, various segments of the same molecule may belong to more than one crystal. As the amount of crystals increases, the movements of the segment of a chain joining two crystals are more limited, impeding conformational changes necessary to crystallize to take place. Thus, perfect crystalline polymers do not exist. However, we may find amorphous and crystalline segments.
Another structural factor affecting the crystallinity degree is the regularity of the polymer. The isotactic chains have some sequences in which the regularity of methyl groups is broken. In the case of Cuyolen Random Copolymers, the regularity is intentionally altered by adding ethylene units throughout the PP chains. In this case, the crystallinity loss results in an increase of the transparency of this type of materials.
Crystal is the fundamental unit in the crystalline structure. Crystals create lamellaes which form espherulites.
As regards processing variables, we must mention the cooling rate of melting as the main factor affecting crystallinity degree. If the cooling rate is high, the polymer solidifies before making the necessary conformational changes for crystallization.
In all transformation processes, the polymer solidifies before the crystallization process ends.
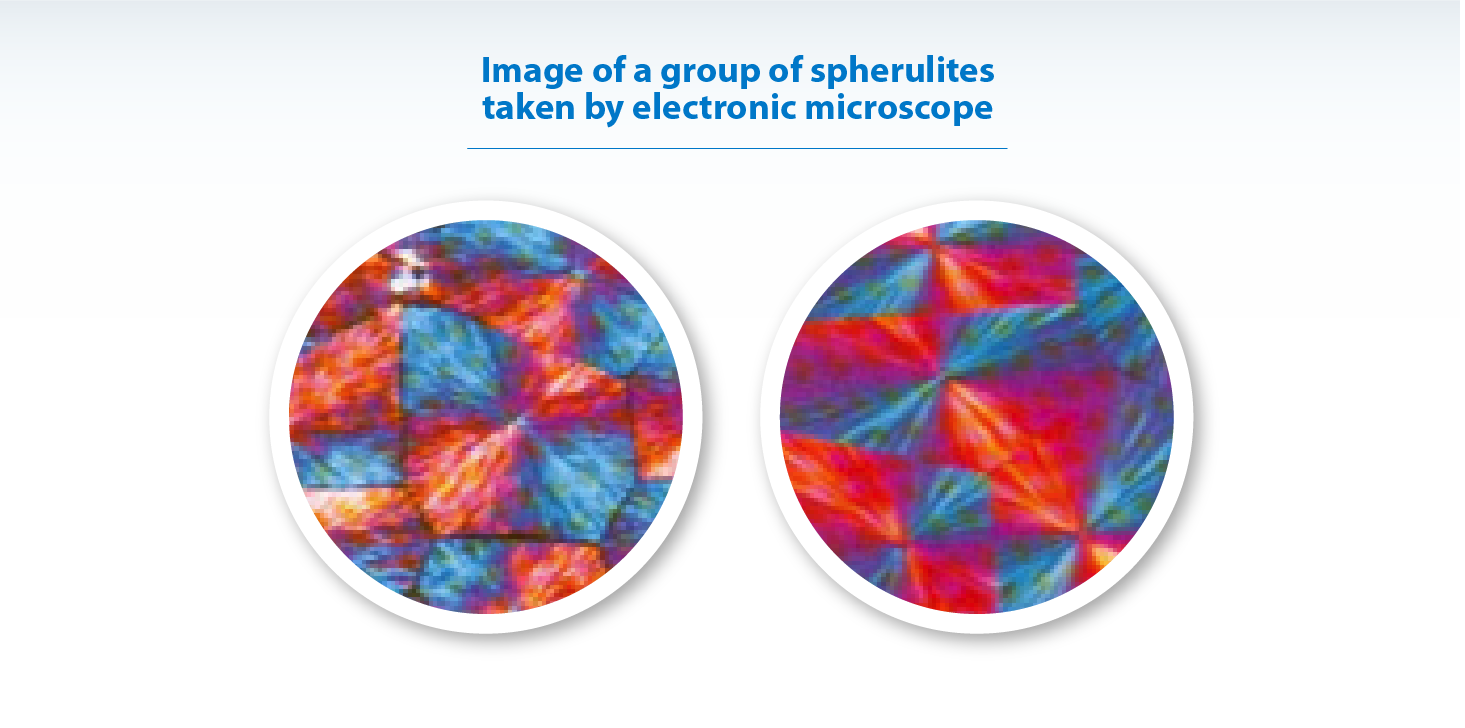
In general terms, a greater degree of average crystallinity results in an increase in the rigidity and in loss of impact since the amorphous regions are those that provide tenacity.
It should be highlighted that materials properties do not depend only on the degree of crystallinity but also on the average size and distribution of the spherulites’ sizes. The addition of a nucleating agent generates smaller spherulites which look more alike (narrows size distribution), and as a result the material improves not only gloss but also transparency.
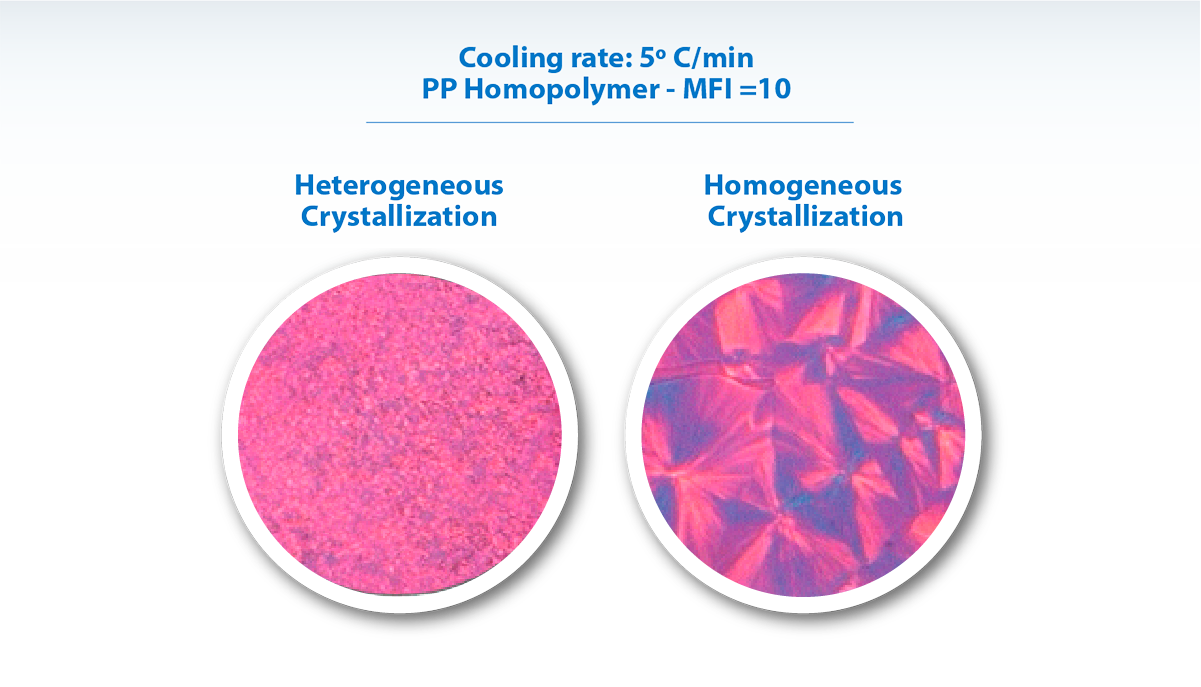